Опубликовано: Июль 15, 2011
Производство целлюлозы Целлюлоза в природе (за исключением хлопка, волоски семян которого содержат 97-98% целлюлозы) не встречается в чистом виде, хотя является главной составной частью растительных клеток и вместе с сопровождающими ее веществами (ннкрустами) составляет твердый остов (каркас) растений. Целлюлоза относится к классу высокомолекулярных углеводов. Выделение целлюлозы связано с большими трудностями, так как она очень прочно соединена с некоторыми веществами, находящимися в древесине. Поэтому в технической целлюлозе, получаемой на заводах, всегда присутствуют в небольшом количестве и примеси. Производство целлюлозы из древесины основано на ее высокой стойкости к определенным химическим соединениям, которые в то же время в известных условиях переводят в раствор менее стойкие вещества, сопровождающие целлюлозу: лигнин, гемицеллюлозы и пр.
В зависимости от применяемых соединений способы получения целлюлозы можно разделить на три основные группы: кислотные, щелочные и комбинированные. В настоящее время разработаны следующие способы: сульфитный, сульфатный, сульфатный с предварительным кислотным или водным гидролизом древесины, сульфитно-щелочной, хлорно-щелочной, азотно-щелочной, гидротропный и др. До последних лет в СССР большее распространение имел сульфитный способ, особенно при получении целлюлозы для химической переработки. Суть этого процесса состоит в обработке древесины раствором слабой сернистой кислоты H2SO3 в присутствии бисульфита кальция Ca(HSО3)2. Замена кальциевого основания (СаО) в варочной кислоте магниевым, натриевым и аммонийным основаниями позволяет улучшить выход, цвет и механические свойства целлюлозы. Основными стадиями технологического процесса любого производства целлюлозы являются: 1) подготовка древесины; 2) приготовление нарочных растворов; 3) варка древесины в варочных котлах и 4) обработка полученной целлюлозы. Хотя целлюлозу можно получать из любой породы дерева, до сих пор ее вырабатывают преимущественно из древесины малосмолистых пород - ели, пихты, бука,-которые можно перерабатывать любым из применяющихся в промышленности способов варки. Смолистые породы (лиственницу, сосну) перерабатывают обычно щелочными методами. Для производства целлюлозы употребляют щепу, полученную из древесных стволов, тщательно очищенных от коры и сучков. Щепа через циклон, сортировку и бункер поступает в котел, где варится с раствором бисульфита кальция, магния, натрия или аммония (сульфитный способ), содержащим избыток сернистой кислоты (раствор содержит 3-6% свободного S02 и около 2% S02, связанного в виде бисульфита). Варка идет в герметически закрытых металлических котлах (объемом 200 -320 кубометров и более), футерованных кислотоупорным материалом, при температуре 135 -150° С и давлении 5-7 атм. Крупную щепу после сортировки направляют на дополнительное измельчение в дезинтегратор. На рис. 21 показана схема подготовки щепы и варки целлюлозы, а на рис. 22 -варочный котел. 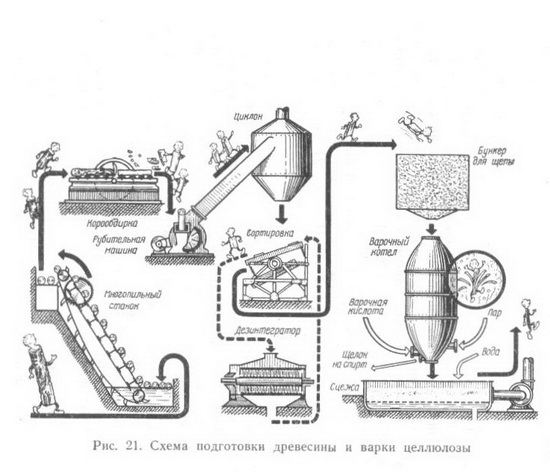 Задача варки заключается в возможно полном извлечении из сырья целлюлозы в неповрежденном виде. Скорость варки и качество получаемой целлюлозы зависят от концентрации варочного раствора, давления, времени, температуры варки, степени провара целлюлозы и других факторов. Общее время варки составляет 6-12 часов. Продолжительность варки, выход и качество получаемой целлюлозы, удельный расход пара и серы зависят от качества исходного сырья, скорости подъема температуры в котле, давления и состава варочного раствора. Быстрое нагревание, высокая конечная температура, использование раствора с повышенным содержанием S02 могут значительно сократить время варки. Для равномерного нагрева и лучшей пропитки щепы применяют принудительную циркуляцию кислоты в котле во время варки. С этой целью варочная кислота засасывается из котла кислотоупорным насосом, проходит через подогреватель и затем снова нагнетается в котел. В ходе процесса варки производят несколько сдувок образовавшихся газов и паров. Сернистый ангидрид SО2, не израсходованный на варку, улавливают для укрепления варочной кислоты, а тепло, уносимое продуктами сдувок, используют для подогрева кислоты. Для этого сдувочные газы и пары из котла направляют на регенерацию SO2 и тепла. Варка целлюлозы сложный процесс. И качество и выход продукта во многом зависят не только от принятой технологии и применяемой аппаратуры, но и от опыта и традиций обслуживающего персонала. После окончания варки давление в котле снижают (сдувкой парогазовой смеси и выпуском образовавшегося раствора, называемого щелоком) до 2-3 ати и содержимое котла удаляют по выдувному трубопроводу большого диаметра в сцежу. На некоторых заводах массу из котла в сцежу вымывают водой. Сцежа - большой резервуар (объем ее в 1,5-2 раза больше объема котла) из железобетона, облицованный деревянными брусьями, с ложным фильтрующим дном в виде решетки. В сцеже щелок отделяется от целлюлозы, и последняя тщательно промывается сначала слабым щелоком, а затем теплой водой. Потери волокна при этом не превышают 0,5%. Промытую целлюлозу разбавляют водой до концентрации 1 -1,2% и перекачивают в очистный цех, где волокно, проходя через сучкоуловитель, песочницу и сортировку, освобождается от сучков, непроварившейся щепы и минеральных загрязнений. Если варка целлюлозы идет в котлах периодического действия, то в очистном цехе вся аппаратура непрерывного действия. Для отделения от массы сучков применяются плоские вибрирующие и барабанные сучкоуловители. При вращении сетчатого барабана (диаметр отверстий 8-11 миллиметров) со скоростью 20-30 оборотов в минуту волокна целлюлозы с водой проходят через сетку, а сучки и непроварившаяся щепа проходят в заднюю коническую часть барабана, откуда и выводятся. Наиболее распространенный вибрирующий сучкоуловитель имеет сито с отверстиями 6 миллиметров, на которое по желобу поступает масса, разбавленная до концентрации 1%. Под воздействием интенсивных и частых колебаний (1450 в минуту) волокна быстро проходят в железобетонную ванну через отверстия, а сучки и непроверенные куски, двигаясь по ситу вверх, переваливаются в сборный ящик. Песочницы изготовляются из дерева или железобетона в виде длинных широких желобов (длина 25-30 м, ширина 1,5 л) с большим количеством поперечных перегородок, наклоненных по ходу движения массы. Если волокно, разбавленное водой до концентрации 0,30-0,35%, движется спокойно, без завихрений, со скоростью 15-18 метров в минуту, то оно не оседает, а оседают более тяжелые минеральные примеси, задерживаемые перегородками на дне песочницы. Вместо песочниц применяют вихревые ловушки, в которых для очистки массы используется центробежная сила. Действие сортировок основано на том, что гибкие целлюлозные волокна, сильно разбавленные водой (до 0,3-0,4%), под воздействием гидравлического напора, вакуума или центробежной силы проходят через небольшие круглые или щелевые отверстия сит сортировки, а непроверенная щепа, пучки волокон и другие отходы задерживаются. Для химической переработки и производства белой бумаги целлюлозу подвергают отбелке и облагораживанию. Основная цель облагораживания - повысить химическую чистоту и однородность целлюлозы. Для этого из нее удаляют остатки лигнина, гемицеллюлоз, золы, смол и улучшают колло-иднохимические и физические свойства этого полуфабриката. В качестве отбеливающих реагентов применяют: хлор или хлорную воду, растворы гипохлорита кальция Са (ОС1)2 или натрия NaCIO, растворы хлоритов NaClOj и NaClOj • ЗНО, двуокиси хлора ClOj, перекиси водорода Н202 и натрия Ха202. Облагораживание целлюлозы проводится растворами едкого натра при обычной или высокой температуре. В нервом случае используется 4-10%-ный раствор NaOH при 20°С в течение 30 минут, а во втором - 1 %-ный раствор NaOH в течение 3 часов при 100° С. При этом в раствор переходит большая часть оставшегося лигнина, золы, гемицеллюлоз, смолистых веществ и продуктов распада целлюлозы, и тем самым повышается содержание основного полезного вещества, называемого альфа-целлюлозой, до 95-98%. Одновременно целлюлоза приобретает такие важные для ее химической переработки качества, как повышенную реакционную способность, необходимую степень полимеризации и более равномерную вязкость. Далее целлюлоза проходит завершающее сортирование, тщательно промывается водой для удаления хлора и кислых продуктов и поступает в размалывающий аппарат, где частицам целлюлозы сообщается способность сцепляться друг с другом. Затем целлюлозу обезвоживают, снова разбавляют водой, после чего она поступает на пресспат, где отливается в бесконечное полотно, подвергаемое прессованию и сушке до содержания влаги 8-12%. Далее полотно целлюлозы разрезают на листы (600x800 мм) и упаковывают. Если целлюлозу транспортируют на другие предприятия, то ее размолу не подвергают. На качество готовой целлюлозы оказывает влияние не только метод производства, но и порода дерева, его возраст, плотность и влажность древесины, наличие в ней гнили, сучков и других пороков. Применение новой технологии получения целлюлозы, т. е. варки на растворимых (аммонийном и натриевом) и полурастворимых (магниевом) основаниях, позволяет на 10-15% увеличить производительность завода, повысить выход волокнистых полуфабрикатов и их прочность. Применение растворимых оснований позволяет вести варку в кислой, нейтральной и щелочной средах в несколько ступеней и из различного сырья получать разнообразные марки целлюлоз. Сульфитная целлюлоза, содержащая небольшое количество лигнина и гемнцеллюлоз, легко отбеливается и облагораживается, широко применяется для химической переработки и в бумажном производстве для изготовления высококачественных видов бумаги и картона. В то же время сульфитный способ производства имеет и ряд недостатков, из которых следует отметить длительное время варки и необходимость кислотоупорной футеровки котлов и кислотостойких трубопроводов. Сульфатный способ производства заключается в варке щепы со щелочным раствором, в состав которого входят едкий натр NaOH и сернистый натрий Na2S, потерн этих химикатов восполняются сульфатом натрия Na2S04. Варка идет в нефутерованных котлах меньшего объема (до 160 кубометров) при максимальной температуре 165-175° С и давлении 8- 10 атм. В результате химического взаимодействия едкого натра и сульфида натрия лигнин вместе с частью гемицеллюлоз переходит в раствор, образуя так называемый черный щелок. Длительность варки при этом методе значительно меньше и составляет 3,5-8 часов. Дальнейшая обработка полученной после варки целлюлозы (очистка, отбелка) примерно такая же, как и при производстве сульфитной целлюлозы. Сульфатный способ производства способствовал расширению сырьевой базы промышленности, так как этим способом можно перерабатывать любую древесину, в том числе отходы лесопиления и деревообработки. Хорошо разработанная система регенерации щелока с последующим возвращением его в производство позволила свести до минимума сброс загрязненных вод в водоемы, который сравнительно велик при производстве сульфитной целлюлозы. Кроме того, сульфатная целлюлоза может быть отбелена до высокой степени белизны при одновременном сохранении механической прочности. Бумага из сульфатной целлюлозы является одной из самых прочных. В то же время сульфатная небеленая целлюлоза более темная и для ее отбелки, которая проводится в несколько ступеней, требуется гораздо больше белящих химических соединений, чем для отбелки сульфитной целлюлозы. В последние годы главным образом в производстве сульфатной целлюлозы все шире применяется непрерывная варка сырья. Применяемые для этой цели варочные аппараты с непрерывной загрузкой исходного сырья и выгрузкой готовой целлюлозы рассчитаны на выпуск 100-400 тонн целлюлозы в сутки. Варочные аппараты по продолжительности пребывания в них сырья могут быть подразделены на две группы: аппараты, в которых сырье находится до 4 часов, и аппараты для скорой варки (до 1 часа). На рис. 25 представлен многотрубный аппарат системы Пандия, имеющий от двух до восьми труб длиной 6-10 метров и диаметром от 300 до 1200 миллиметров и расположенных друг под другом. Конец каждой трубы соединен с началом другой. Внутри каждой трубы вращается шнек, перемещающий сырье к выходу из трубы и имеющий строго регулируемое число оборотов. Варочный щелок и пар при варке древесной щепы подается при выходе щепы из питателя. Пар поступает в первую и иногда во вторую варочную трубу. Условия варки: давление до 12 ати температура 170-190° С. Масса из варочного аппарата выводится с помощью разгрузочного устройства в выдувной резервуар. В зависимости от условий варки при сульфатном методе производства можно получить целлюлозу разного выхода (в процентах по отношению к исходной древесине): Растворимая................ 30-37 Высокого выхода....................... 55-62 Нормальная ............. 42-48 Полуцеллюлоза....................... 65-90 Повышенного выхода .... 53-55 Максимальная температура варки для каждого вида целлюлозы устанавливается опытным путем. Целлюлоза высокого выхода (на 12-14% больше, чем при варке обычной целлюлозы) производится при сокращенном времени варки и более низкой конечной температуре, при этом лигнин и гемицеллюлозы растворяются варочным раствором в меньшей мере, чем при обычной варке. Расход древесины сокращается примерно на 20%. Таким образом, для выработки 1 млн. тонн целлюлозы высокого выхода нужно почти на 2 млн. кубометров древесины меньше, чем для получения такого же количества обычной целлюлозы. Выход полуцеллюлозы на 20-40% больше выхода обычной сульфатной целлюлозы, так как только около половины лигнина и одной трети гемицеллюлоз удаляются во время варки из древесины. Для производства полуцеллюлозы можно использовать и низкокачественную древесину. Количество расходуемой древесины уменьшается при этом почти на 40%. Прочность полуцеллюлозы примерно равна прочности хвойной сульфитной целлюлозы, которую она успешно заменяет в производстве бумаги. При сульфатном способе производства высококачественной целлюлозы, идущей на химическую переработку, древесину перед варкой подвергают гидролизу (пропарке сырья паром, водной варке, варке со слабым раствором сильной кислоты). Во время такой обработки из древесины удаляется большая часть гемицеллюлоз, чем и облегчается последующий процесс обычной сульфатной варки. Из щелочных способов можно отметить и натронный способ, при котором варочный щелок содержит NaOH, а потери щелочи возмещаются добавкой соды. Выход и прочность изготовляемой этим способом целлюлозы значительно ниже, чем сульфатной, но полуцеллюлозы из лиственных пород древесины, полученные холодно-натронным способом, обладают рядом ценных свойств. Для получения полуцеллюлозы из лиственных пород и однолетних растений используют также среднюю соль сернистой кислоты (Na2SOa) в присутствии щелочи, называемой буфером (например, №2СОз, NaHC03, NaOH). Этот способ варки носит название нейтрально-сульфитного. Щелочь при такой варке (в паровой фазе при 160 или 175°С с предварительной пропиткой при 100° С) растворяет преимущественно лигнин. За последние годы внедряются и комбинированные способы производства целлюлозы. Так, при кислотно-щелочном способе древесную щепу обрабатывают в котле последовательно раствором бисульфита натрия в течение 5-6 часов при 150° С и после удаления образовавшегося щелока- 1-2 часа раствором карбоната натрия при 166° С. Применяется также хлорно-щелочной способ. В этом случае солому или стружку (осина - тополь) последовательно обрабатывают щелочью и газообразным хлором. Для удаления продуктов превращения лигнина и других веществ, сопровождающих целлюлозу, массу вновь обрабатывают разбавленным раствором щелочи. Выход целлюлозы по этому способу достигает 38-45%. Могут быть применены также азотно-щелочной способ и варка в присутствии гидротропных реагентов. По первому способу растительное сырье нагревают в течение часа с азотной кислотой концентрацией 2-4% и после промывки горячей водой - щелочью примерно такой же концентрации. Выход целлюлозы 40-43%. По второму способу варку ведут в присутствии концентрированных (40-50%-ных) водных растворов органических солей (натриевых солей салициловой кислоты, бензойной кислоты, толуолсульфокислоты или ксилолсульфокислоты), которые легко переводят лигнин в раствор. Чем выше температура и концентрация соли, тем больше лигнина переходит в раствор. При разбавлении полученного раствора водой большая часть растворенного лигнина выпадает в осадок. Сравнительная характеристика различных видов технической целлюлозы приведена в табл. 3. Характеристика различных видов технической целлюлозы Древесная масса - волокнистый полуфабрикат из древесины с максимально возможным выходом. Такая масса успешно используется в производстве газетной бумаги и картона различных марок. Обычную белую древесную массу получают механическим истиранием хорошо очищенных бревен длиной 125 сантиметров (баланса) в машинах, называемых дефибрерами, на вращающихся цилиндрических камнях с шероховатой поверхностью в присутствии воды. Для древесной массы характерны сравнительно низкая механическая прочность, непрозрачность и пухлость. Химическую древесную массу получают или из баланса, пропитанного химикатами, истиранием на дефибрерах или из пропитанной щепы путем ее размола на рафинерах различного устройства. Выход массы составляет 85%. Прочность ее в 2-3 раза выше прочности обычной белой древесной массы. Для получения тонны химической древесной массы необходимо израсходовать всего 2,5-3,0 кубометра древесины (почти всех пород), т. е. в 2 раза меньше, чем при производстве целлюлозы (табл. 4). Расход сырья, энергии и воды на тонну продукции
На Сухонском комбинате довели расход древесины на каждую тонну целлюлозы до 5 кубометров, а количество химикатов-до 120 килограммов вместо прежних 520 килограммов. Анализ показывает, что если повысить выпуск целлюлозы с каждого кубометра котла хотя бы на 5-6 килограммов в смену, то это даст стране дополнительно более 100 тыс. тонн целлюлозы в год. Прим. Внимание! Формулы могут быть искажены, - см. источник!. источник: А. Авербух, "Что делает химия из древесины", Москва, издательство "Лесная промышленность", 1970 год
От: LidiaZaiceva,   -
-
Скрыть комментарии (отзывы) (0)
Похожие темы:
« Вернуться
|